Weinig Powermat 1500 Moulder
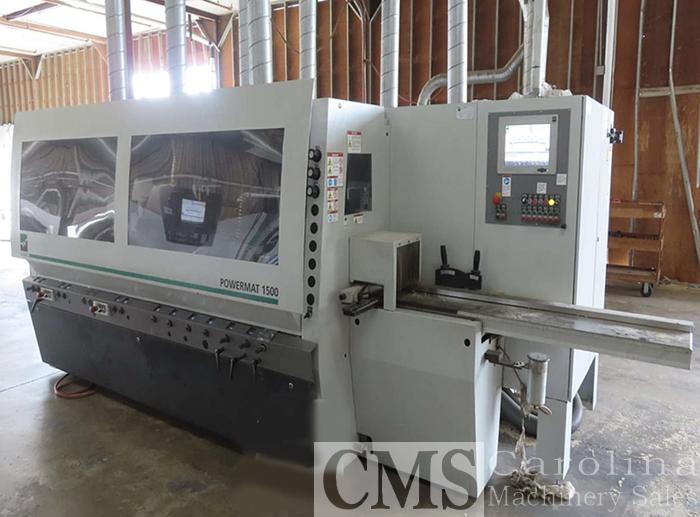
Specifications
Manufacturer | Weinig |
Model | Powermat 1500 Moulder |
Stock Number | 010960 |
Description
Weinig Powermat 1500 Moulder
7-head Machine
Manufacturer specs (to be confirmed):
Operating voltage (single) 460 Volt, 60 Cycles
Tool arrangement no. 013
Working width 20 - 230 mm
FIRST BOTTOM - Motor 11 KW (15 HP) / 1 13/16" / 6000 rpm
Marathon coating for table insert
RIGHT VERT - Motor 11 KW (15 HP) / 7000 rpm
Diameter 40mm
Setting range axial 80mm
LEFT VERT - Motor 11 KW (15 HP) / 8000 rpm
Vario hood (2 axes)
Pressure shoe in front of left, incl. 2 lateral rollers, spring-mounted
Setting range of the feed rollers opposite left tool holder
Pressure roller from above, pivoting, spring loaded
Axial / Radial CNC-controlled adjustment
SECOND RIGHT - Motor 11KW (15 HP)
Fence lip before and after the right vertical spindle
Axial / Radial CNC-controlled adjustment
FIRST TOP SPINDLE-MOTOR 22 KW (30HP) - 7000 rpm
Vario Hood (2 axes)
Split pressure shoe in front of top spindle with
Axial / Radial CNC-controlled adjustment
SECOND TOP - Motor 18.5 KW (25HP)/ 7000 rpm
Split pressure shoe in front of top spindle
Axial / Radial CNC-controlled adjustment
Top spindle prepared cassette system.
LAST BOTTOM - Motor 22 KW (30 HP) / 7000 rpm
Adjustment range axial & radial
FEED SYSTEM - Motor 7 KW (9.5 HP) / 5 - 40 m/min.
Feed roller in front of 1st bottom, pneumatic up-down
Electrical up-down adjustment of the feed bar
Two interior lights in the safety hood
Remote Lock out / Tag out
Lateral pressure roller at the infeed table, spring-mounted
Guiding fence after the left vertical spindle 6 mm thick
PowerCom Plus
Improved sound insulation
*
MACHINE CHANGE: 06.10.2019 - Please be aware that the VarioHood assembly on the
1st Top Spindle was moved to the 2nd Top Spindle position. The 2nd Top Standard
Hood was moved to the 1st Top Spindle Position. This move will impact the parts
relating to the Aspiration Hood, ChipBreaker and Pressure Shoe elements. Please
use caution when looking up replacement parts. This machine change was performed
by WUSA technicians