Kahl 250 HP Pellet Mills
Sold
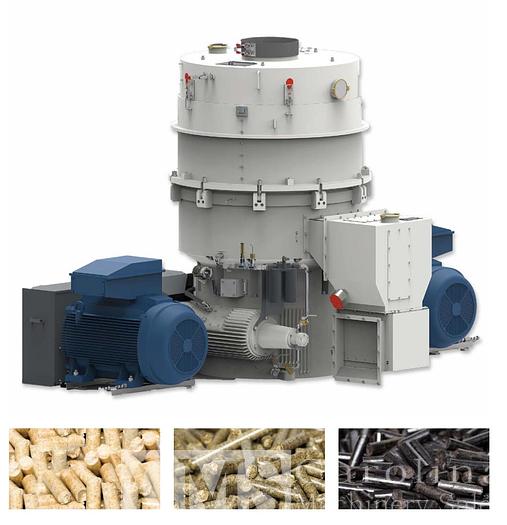
Specifications
Manufacturer | Kahl |
Model | 250 HP Pellet Mills |
Stock Number | 010330 |
Description
This system is part of a project that never took off. The machines are new, never installed:
- (6) Kahl 39-1000 Pellet Mills
- 200 kW (268 HP) Motors: Two are wired at 460v, four at 575v. The other 4 can be rewound for a fee.
Manufacturer specs (to be confirmed):
Equipment List
6 Pelleting press type flat die 39-1000
Consisting of:
575V, 60 Hz 110 V AC 24 V DC
- Divided cast iron case provided with cooling fins in the gear zone
- Venting port in pellet mill middle part
- Dust and inlet hood with product distributor and a venting port
- Main shaft with thrust and radial bearings
- Pan grinder head with scrapers and pan grinder rollers made of flame hardened steel
- Temperature measuring of the die
- Spring assembly, stainless steel
- Spacer rings
- Discharge unit with special scrapers
- Worm gear turning in oil bath, worm wheel made of special bronze, hardened worm
- shaft
- Fan pulley
- Oil pump to lubricate the main bearings, with oil filter, pressure device and thermometer
6 Three phase induction motor
For the drive
- Voltage: 575V
- Motor power: 200 kW at 1,800 RPM
- Drive shaft 90x170mm
- Protection class: IP65, motor type B3
- Bearing suitable for 18 kN @ x=136mm
- Stainless steel nuts and bolts
- 12 tension rails
• Two pieces per motor
6 Drive accessories for the pelleting press
Consisting of:
- V-belt pulley
- V-belts
- V-belt guard, steel construction, lateral walls with special air guiding plates,
- indispensable for pelleting press cooling
- 6 Roller gap control, type Distamat
- For continuous adjustment of the roller head via the hydraulic nut Consisting of:
- Hydraulic system for the press
- Valve control
- Electronic elements for transforming the measuring signals
- Output: 4 – 20 mA = 0-5 mm
- 6 Central slip ring seal air cleaning
- For protection of the pan grinder roller slip ring seals during operation of the press Consisting of:
- Air distribution with piping and coupling
- Hose with central air connection to the pressed air
6 Oil coolers for the press
Designed as oil-to-air heat exchanger Consisting of:
- Oil-to-air heat exchanger
- Oil pump
- Hose connections
- Temperature controller
- 6 Press outlet box 39-1000
- Stainless steel design Equipped with:
- Reversing flap
- Inspection opening
- Control socket
- Aspiration connection, venting port
- Pile up indicator
- 1 Spare roller head for the 39-1000
- Spare, for easy and quick exchange of the roller head
- 6 Automatic press control, type EAPR
- Allen Bradley
- For automation of pelleting line
- Enclosed design, wired ready for connection according to IP 65 Consisting of:
- Control and monitoring of all drives and units belonging to the line
- Load dependent control of the pelleting press
- Min/Max current monitoring of the pelleting press
- Slippage monitoring of the pelleting press
- Throughput control (t/h)
- Visualization of the line on a graphic operator panel
- Preselection of the process parameters at the OP
- Fault and alarm messages at the OP
- Start/stop buttons for direct activation of the main drives
- PLC control system with interlockings for manual and automatic mode
- Analog display for press current and hydraulic pressure